How Can Cleaning with Vapor Degreasers Save Electricity?
The energy efficiency of vapor degreasing is one of the main advantages of solvent cleaning when compared to water cleaning. Water cleaning uses a great deal of electricity while solvent cleaning uses far, far less. For customers in locations where electricity is expensive, vapor degreasing is the most energy efficient and affordable way to clean. Additionally, burning fossil fuels to create electricity is one of the primary contributors to global warming, so saving electricity is good for your budget and the planet.
Energy-Intensive Aqueous Cleaning
There are four design features in every aqueous cleaning system which make them very energy-intensive. These are:
- Power to the numerous, high-pressure pumps which move the water around the machine, and the machines can be huge;
- The energy it takes to heat the cleaning water,
- The energy it takes to dry the parts, and lastly
- The energy it takes to treat and purify the water for re-use or disposal.
All of this additional work is required because of the inherent nature of the molecule of water. Basically, water has both a high surface tension and a high latent heat of evaporation. These are characteristics that no amount of fancy engineering can change. Consider these three fundamental characteristics:
High surface tension is a problem for water cleaning. It stops the water from going into tight spaces. That’s why users first need (a) to heat the water, and then (b) then they need to use additives to boost the cleaning power and reduce surface tension, and finally they need (c) those big pumps to spray the water-and-additive mix in to tiny components.
Then, the high latent heat of evaporation causes still more problems because this makes water a slow-drying cleaner. It takes a lot of heat and big, energy-sucking air knives to remove the aqueous residuals from the components.
At this point, the water has picked up the contamination — in addition to the cleaning additives, the water may now be holding oils, fluxes, lead from the PCBs and so on. That water, the additives and the contamination now must be treated in a waste-water treatment system to re-purify the water. Normal treatment facilities include reverse-osmosis systems and multiple stacks of de-ionizing filters. Obviously, this takes more electricity and more pumps to move the waste water through these cleansing processes.
Energy-Efficient Vapor Degreasing
In general, modern, nonflammable solvents have low surface tension, low viscosity, high density and low latent heat. This means they’re going to clean more easily, with less heating, fewer pumps, no air knives and so on. There is no water to heat, which saves electricity. Instead the solvent is heated to just above room temperature, which takes very little electricity.
- There are no big pumps required to push the solvent around, which saves electricity. Instead, the solvent moves by gravity.
- There are no blowers or “air knives” on vapor degreasers, which saves electricity. The solvent is retained inside the machine and the parts being cleaned come out dry. (In fact, even motorized fans and fume hoods are not recommended near vapor degreasers because it increases solvent losses, so electricity is saved there, too.)
- There is no waste treatment facility required, which saves electricity, because the degreaser is automatically, inherently and continuously re-purifying and re-distilling the solvent.
- There is no humidity added to the factory environment, so air conditioning and environmental loads are reduced.
The net result is that the typical vapor degreaser uses about 30 amps or power when cleaning and one-tenth of that energy in stand-by (night) mode; many of the smallest machines use standard household electrical connections! This contrasts with water-cleaning systems with power consumption is measured in hundreds and thousands of amps, and often require 440 volt circuits and big power panels to manage the electrical load.
This is one case where simpler really is better.
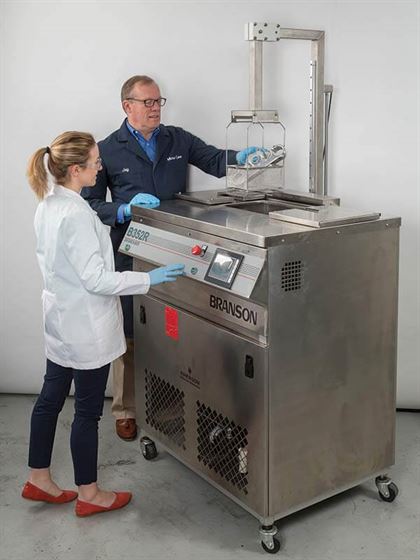