How Can I Cost-Justify the Trigger Grip System?
It’s a funny thing — MicroCare’s biggest competitor is not some other aerosol company. Our biggest competition is cheap alcohol in a small bottle. “Dip-and-brush” cleaning is cheap to buy, but more expensive to use. In our opinion, dip-and-brush cleaning at the benchtop is an expensive way to get poor results.
Remember that alcohol is hygroscopic, which means it absorbs water from the air. This dilutes it, and weakens its ability to clean.
Alcohol also is often diluted with water by 20% or more, simply to keep costs down. This dramatically reduces its cleaning strength. So using a bad process with a weak cleaner leads to expensive cleaning.
If people want the lowest total cost per part cleaned then everybody should use the TriggerGrip™ dispensing system. With each TriggerGrip™ tool customers will get better, faster, more reliable cleaning at a lower cost per-part- cleaned.
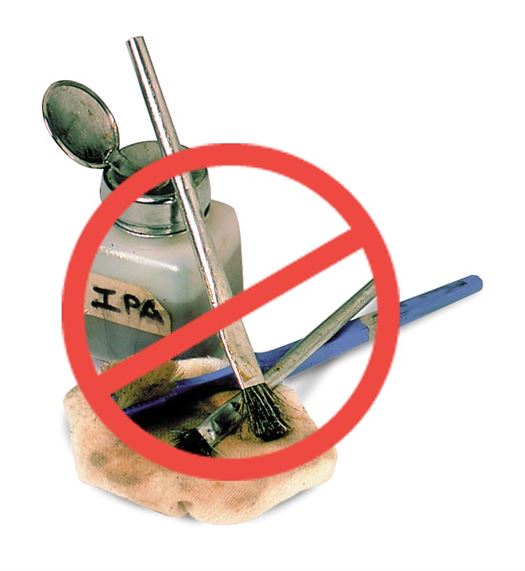
The High Costs of Dip-and-Brush Cleaning
You see, its not the cost of the solvent that is the issue here — it’s the cost of wasted time. The TriggerGrip™ dispensing system forces techs to use all four steps of the cleaning process — wet, scrub, rinse and dry. Because the techs use all four steps, the results are better, safer, faster and less expensive. This results in substantial savings.
For example, MicroCare products typically cost $0.50 – $1.00 per day to use. With a TriggerGrip™ dispenser on their workbench, MicroCare helps the tech do more cleaning in less time. This time-saving is typically about 30 minutes per day per technician. So if the company has 15 techs in the rework area, MicroCare can save 30 minutes times 15 people — that’s about 8 hours per day. So the company gets one technician work-day for free, if they use MicroCare.
Here’s another way to figure it out: How many pieces of rework does each tech do in a day? What is the value of that rework? Usually it sounds something like this: “Well, our techs typically rework 60-80 pieces per day, and each box that leaves the factory is worth $50 profit to the company.” In an eight-hour day, that works out to roughly ten pieces per hour, or $500 gross profit per technician per hour. Now do the math. The TriggerGrip™ system saves 30 minutes per tech per day, which is 5 pieces, at $50 each piece, it produces a total of $250 additional profit per tech per day. With 15 techs, the TriggerGrip™ dispensing system will save enough time to rework $3,750 more products and produce more profit each day.
Or, putting it another way, NOT using the TriggerGrip™ dispensing system burdens the company with $3,750 worth of extra cleaning costs every single day.
To put it still another way: buying cheap alcohol may cost you 50¢ per benchtop per day and the TriggerGrip™ dispensing system might cost you $1 per day. But because dip-and-brush cleaning is slow and the quality is poor, your techs waste a lot of time doing it. This lost productivity costs you hundreds of times more than the money you save with cheap solvent.
So it’s not the cost of the can of solvent — it’s the lost profits, the hidden costs, and the lost productivity of your technicians that make MicroCare a great choice for benchtop cleaning.
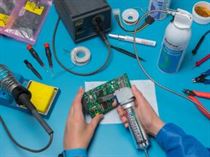
The TriggerGrip™ cleaning system connects to a MicroCare aerosol can and delivers fast, better and safer benchtop cleaning