Cleaning No-Clean Flux Residue: When, Why, and How?
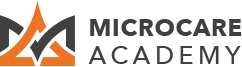
Objectives
By the end of this lesson, you will understand:
- The importance of removing flux residue and other contaminats from PCBs
- Why no clean fluxes were introduced
- How to clean no clean fluxes using the best fluids and methods
The Role of Solder Fluxes in PCB Assembly
The Pre-No Clean Flux Era
The Montreal Protocol and Environmental Concerns
The Development of No-Clean Fluxes
In response to these environmental and regulatory pressures, no-clean solder fluxes were developed as a revolutionary solution. No-clean fluxes were designed to eliminate the need for post-soldering cleaning by leaving minimal, non-corrosive residues on the board. This innovation not only addressed environmental concerns but also helped manufacturers save time and costs associated with the cleaning process. With no-clean fluxes, the PCB assembly process became more streamlined, allowing manufacturers to meet stricter environmental regulations while maintaining or even improving production efficiency. This shift was instrumental in driving the electronics industry toward greener and more sustainable manufacturing practices.The Catch with No-Clean Flux
While no-clean fluxes offer the convenience of eliminating post-soldering cleaning, they come with a significant caveat: specific heating requirements. No-clean fluxes contain chemical activators that must be properly oxidized during the soldering process. This oxidation is critical to prevent harmful residues from remaining on the PCB. For the flux to fully activate and neutralize, the soldering temperature must be precisely controlled. If the flux is not heated to the appropriate temperature, the activators may not break down completely, leaving behind residues that can cause corrosion, electrical failure, or other issues over time.
Challenges in Heating Profiles
Achieving the correct heating profile can be particularly challenging in certain PCB assembly scenarios. For instance, hand soldering often introduces variability in temperature control, leading to incomplete activation of the no-clean flux. Additionally, densely packed PCBs with multiple components and varying heat sinks can create uneven heat distribution during the soldering process. In such cases, certain areas of the board may not reach the necessary temperatures, resulting in pockets of unreacted flux. These residues, though minimal, can still compromise the long-term reliability of the circuit, especially in high-performance or sensitive electronics.
The challenges with heating profiles make it essential for manufacturers to carefully monitor and control the soldering process when using no-clean flux. In automated environments, such as reflow soldering, advanced temperature control systems can help ensure uniform heating across the entire board. However, in manual or mixed-component processes, achieving consistent results can be more difficult. Understanding the heating requirements and potential risks of no-clean flux residues is crucial for ensuring high-quality, reliable assemblies.
Reasons to Clean No-Clean Flux Residue
Although no-clean flux is designed to eliminate the need for post-soldering cleaning, there are several scenarios where cleaning the residue is still essential.
- Signal Integrity: Impact of flux residues on signal transmission and overall assembly performance. One key factor is signal integrity. Residual flux on a PCB can interfere with signal transmission, especially in high-frequency or sensitive circuits. Even trace amounts of residue can alter the impedance of the traces, leading to signal distortion, data loss, or interference. As electronics become more complex and miniaturized, with higher data rates, the impact of any contamination—no matter how small—can have a significant effect on the overall performance of the assembly.
- Conformal Coating Adhesion: Importance of cleaning for optimal coating adhesion. Is another critical reason to clean no-clean flux residue. Many electronics assemblies are coated with conformal coatings to protect against environmental factors like moisture, dust, and chemicals. If flux residues are left on the board, they can prevent the coating from adhering properly to the surface. Poor adhesion can lead to areas of the PCB being inadequately protected, which can result in premature failure or damage to the components. Ensuring that no-clean flux residue is removed before conformal coating is applied helps maintain the integrity and longevity of the protective layer.
- Aesthetic Considerations: How visible residues affect the quality and perception of assemblies. also play a role in the decision to clean no-clean flux residue. Visible residues, even if they are not electrically harmful, can give the impression of poor workmanship or low-quality assembly. Customers and inspectors often expect a clean, professional appearance, particularly in industries where reliability is paramount. Visible flux can detract from the perceived quality of the product, which could impact customer satisfaction and brand reputation.
- Quality Control: Challenges posed by flux residues during inspections and the benefits of thorough cleaning. during inspection can be complicated by flux residues. Automated optical inspection (AOI) systems and manual visual inspections may flag flux residues as potential defects, causing unnecessary rework or delays. Thoroughly cleaning no-clean flux residues can streamline the inspection process, reduce false positives, and help maintain consistent product quality. In many cases, the decision to clean no-clean flux residues is driven by a combination of technical performance, aesthetic, and quality control considerations.
How to Clean No-Clean Flux Residue
When it comes to cleaning no-clean flux residue, one of the most critical factors is selecting the right cleaning fluid. No-clean flux formulations vary widely, with each designed to provide specific soldering performance, and this means that not all cleaning fluids are effective for every type of residue.
- Importance of Matching Fluid to Flux Chemistry: Variations in flux formulations and the need for appropriate cleaning fluids. The chemical composition of the flux—whether it contains rosin, resin, or synthetic activators—can influence the choice of cleaning solvent. If the cleaning fluid is not matched correctly to the flux chemistry, it may not fully dissolve or remove the residues, potentially leaving behind contaminants that could impact the performance and appearance of the PCB. Thus, understanding the chemical makeup of the flux is key to choosing an effective cleaner.
- Supplier Consultation: Importance of working with cleaning fluid suppliers for compatibility and effectiveness. Because of these variations, supplier consultation is essential in the process of selecting a cleaning fluid. Working closely with cleaning fluid manufacturers or suppliers ensures that the chosen solvent is compatible with both the flux and the substrate materials of the PCB. Suppliers can offer tailored advice, including the best fluid for the specific flux formulation, the material compatibility, and the optimal cleaning method, whether manual or automated. In many cases, suppliers can also provide sample fluids for trial cleaning runs, helping manufacturers confirm that the cleaning process will meet both cleanliness and safety standards.
Additionally, suppliers are often well-versed in industry regulations, environmental compliance, and safety requirements, which helps manufacturers avoid potential issues with hazardous chemicals or processes. Engaging with a supplier early in the cleaning process ensures a thorough understanding of how the fluid will interact with the flux residue, how efficiently it will clean, and whether it aligns with the manufacturer’s production and environmental goals.
Cleaning Methods
There are two primary methods for cleaning no-clean flux residue: manual benchtop cleaning and automated vapor degreasing. Both have their advantages depending on the scale of operations, type of contamination, and production needs.
Manual Benchtop Cleaning: Manual benchtop cleaning is a hands-on approach typically used in smaller operations or for spot cleaning after assembly. The process involves the use of cleaning solvents, brushes, wipes, or swabs to manually remove flux residues from specific areas of the PCB. Operators apply a cleaning fluid—often an aerosol or liquid solvent—directly to the affected area, using tools like lint-free wipes or specialized brushes to scrub away the residue. After cleaning, any remaining solvent is wiped away, and the part is left to air-dry.
For more efficient and precise manual cleaning, the TriggerGrip™ Dispensing System offers several benefits. This system integrates cleaning fluid with a mechanical trigger, allowing operators to control the amount of solvent dispensed directly at the contamination site. By delivering fluid right where it's needed, TriggerGrip reduces the waste typically associated with aerosol cans and open bottles of cleaning solvents. It also limits exposure to solvents, making the process safer for the operator by reducing solvent fumes and skin contact. Additionally, the system minimizes solvent evaporation, allowing for more thorough cleaning with less fluid, ultimately lowering cleaning costs.
The TriggerGrip system is especially beneficial for tasks that require precision and repetition. Its ergonomic design reduces hand fatigue, enabling operators to maintain consistency and accuracy during extended cleaning sessions. By optimizing the cleaning process, the TriggerGrip system can improve the overall efficiency of manual benchtop cleaning while reducing solvent consumption and environmental impact.
The advantage of vapor degreasing is its efficiency and uniformity. It is an automated process that can handle large volumes of parts quickly, making it ideal for batch cleaning in high-production environments. Vapor degreasing also provides consistent, repeatable results with minimal operator involvement, reducing the risk of errors. Additionally, since the solvent is continuously distilled and recycled, it is a cost-effective and environmentally friendly solution compared to aqueous cleaning methods, which may require large amounts of water and energy.
One key consideration in vapor degreasing is selecting a compatible cleaning solvent that aligns with the flux chemistry and part materials. The cleaning equipment must also be properly maintained to ensure efficient solvent recovery and prevent contamination buildup. Overall, vapor degreasing is a powerful tool for removing no-clean flux residues, particularly for manufacturers looking for an automated, scalable cleaning solution.
Conclusion
Balancing Innovation with Quality: Balancing innovation with quality is critical when addressing the challenges of no-clean flux residues in PCB manufacturing. While no-clean fluxes are designed to minimize the need for post-soldering cleaning, certain scenarios still require flux removal to maintain optimal performance, reliability, and aesthetics. Residues left behind can negatively impact signal integrity, hinder conformal coating adhesion, and create visual defects that reduce the perceived quality of the product. Knowing when to clean these residues ensures that PCBs not only meet technical requirements but also uphold industry standards for durability and appearance.